Überwachung des Dosierungs und Gewichtssystems
Systembeschreibung
Ein großes Unternehmen der Lebensmittelproduktion von Backwaren, das seine Produkte für den Export verkauft, hat ein Überwachungssystem für das Wiegesystem beantragt. Dieses Subsystem wurde als Teil der Schaffung eines integrierten Systems zur Verfolgung des Durchgangs von Produkten entlang der technologischen Kette erstellt.

Waagen sind der Ausgangspunkt der technologischen Produktionskette von Backwaren. Bei Fehlern beim Dosieren des Bauteils kann die Qualität des Endprodukts nicht sichergestellt werden. Detaillierte Information zum Dosierungsverlauf ist der Schlüssel zur Ermittlung der Ursachen möglicher Fehler in der Arbeit und Maßnahmen zu deren Beseitigung. Die Produktion verwendet ein ziemlich umfangreiches Rezeptsortiment (Hunderte verschiedener Typen), nachdem die Installation des Mischers funktionieren sollte.
Aufgrund der Vielzahl von Rezeptarten und deren ständigen Änderungen werden nur wenige Grundrezepte im Speicher der Bediengeräte abgelegt, die ggf. vor dem Mischen vom Bediener korrigiert werden. In der Regel wird eine Reihe ähnlicher Dosierungen durchgeführt, jedoch können während Dosierungen Abweichungen der Wassertemperatur (die stabil sein sollte) und andere Parameter, Notstopps aufgrund von Mechanismenversagen, Anhaften einer großen Waage an Waagen usw. auftreten.
- Das vorhandene Protokollierungssystem war unzuverlässig und veraltet, was äußerst unbequem war.
Um die Zuverlässigkeit, die Bequemlichkeit der Analyse von Berichten und den Grad der Kontrolle des Wiegeprozesses zu erhöhen, hat das Unternehmen beschlossen, das System auf folgende Weise zu modernisieren:
- Aufzeichnung des Prozesses, so dass für jede einzelne Dosierung eine Verschreibungsaufgabe gesehen werden kann und die tatsächlichen Massen der dosierten Komponenten zusammen mit den Dosierungsfehlern, den Start- und Stoppzeiten für die Dosierungen jeder Komponente, den Pausen zwischen den Phasen des Prozesses und anderen Informationen.
- Berichte sollten zwei Ebenen haben, d. H. Eine Liste sollte die Anzeige kurzer Informationen mit Hinweis auf das Vorhandensein / Fehlen eines Unfalls ermöglichen, und die zweite wäre ein detaillierter Bericht mit erweiterten Informationen.
- Speichern Sie die Daten für eine spätere Analyse lange Zeit. Da die hergestellten Produkte eingefroren waren, gelagert wurden und nach längerer Zeit dem Verbraucher übergeben werden konnten (in der Regel für den Export), ist es im Falle einer Reklamation erforderlich, die Ursache des Problems anhand der archivierten Daten ermitteln zu können.
Quellsystemstruktur
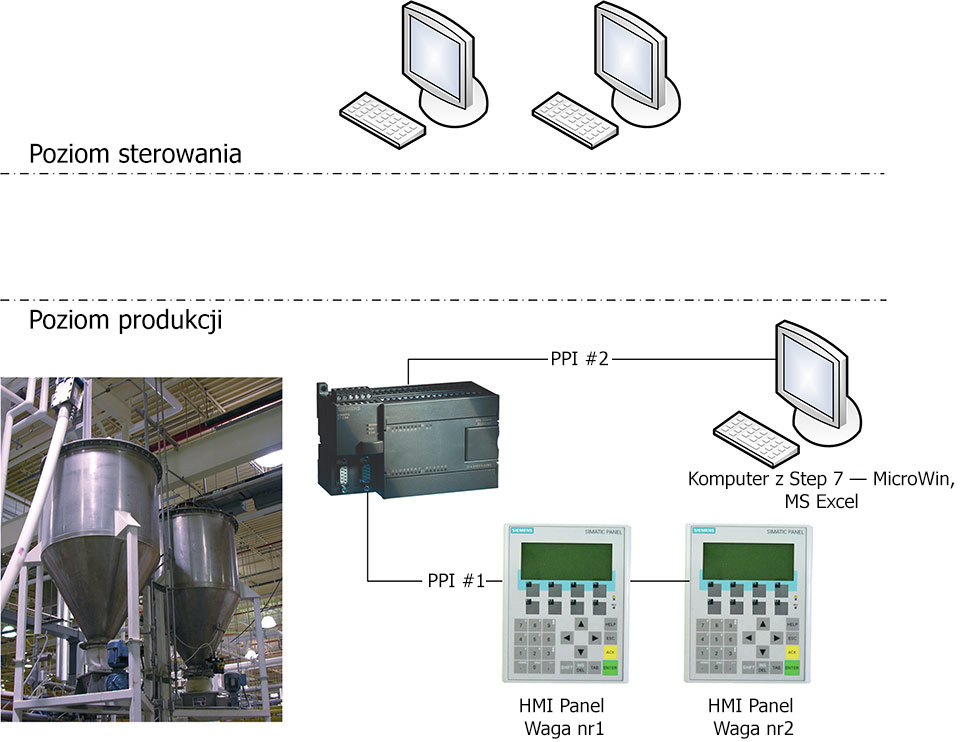
- Schaltschrankgewichte №1 und 2, einschließlich:
- SPS Siemens S7-200 1 Stck.
- OP-77 Bedienfeld 2-tlg.
- Computer mit installierter Software Schritt 7 – MicroWin, veraltete Version von MS Excel
Nachteile des bestehenden Systems
- Die Registrierung wurde in der SPS selbst implementiert, wobei das Programm alle erforderlichen Signale mit Zeitstempeln im SPS-Speicher protokollierte, und eine fest angeschlossene Workstation mit Siemens MicroWin-Software führte den SPS-Speicher als DAT-Dateien auf die Festplatte aus. Bei Bedarf wurden die Daten dann manuell in MS Excel importiert und per Makro in das gewünschte Formular konvertiert.
- Diese Aufzeichnungsroutine beanspruchte den gesamten freien Speicherplatz der SPS, was den Änderungsprozess beim Einrichten der Ausrüstung äußerst kompliziert machte und manchmal sogar zum Stoppen der SPS führte.
- Die manuelle Suche nach Dateien, die für die Analyse und die Konvertierung in einen Bericht erforderlich sind, war unbequem. Makros wurden für die veraltete Version von MS Offi geschrieben und funktionierten einfach nicht für die neuen Versionen. Daher konnten sie nur auf einem separaten PC mit der alten Version ausgeführt werden.
- Die Entwicklung eines neuen Protokollierungssystems mit einem großen Archiv (bequemes Anzeigen und Drucken usw.) ist eine große Herausforderung. Die Produktion läuft kontinuierlich in drei Schichten. An einem dedizierten Tag für Wartungsarbeiten haben die Mitarbeiter einfach keine Zeit, eine Lösung für die Umsetzung dieser Aufgabe zu entwickeln und zu implementieren. Die Produktion ist nicht akzeptabel.
Idealne dla tego systemu byłoby rozwiązanie zorientowane na podobny problem, które pozwala bez programowania na niższych stopniach w trybie konfiguracji zrealizować odpytywanie PLC i zbudować wymagane raporty, które można wygodnie przeglądać, znajdować problematyczne dozowanie i otrzymywać dla nich szczegółowe sprawozdanie, a jeśli to konieczne, otrzymywać dodatkowe informacje analityczne, takie jak wykresy historyczne, najlepiej niezależnie od platformy oprogramowania, na przykład w przeglądarce internetowej.
Projektkonfiguration nach der Verwendung von WebHMI
Die integrierten Funktionen von WebHMI ermöglichten die schnelle Lösung des Archivierungsprotokolls:
- Die S7-200-SPS wurde über eine RS-485-Schnittstelle mit dem PPI-Austauschprotokoll verbunden
- Mithilfe des integrierten WebHMI-Mechanismus für Ereignisse und Skripts, Visualisierungstools, ohne das SPS-Programm zu beeinträchtigen, werden die erforderlichen Berichtstypen und Verlaufsdiagramme konfiguriert
- Die Daten werden über eine webbasierte Schnittstelle bereitgestellt – Mitarbeiter der Produktionsabteilung kommen vom Browser über das lokale Netzwerk zur WebHMI und können einen Bericht für das erforderliche Zeitintervall anzeigen oder drucken. Diese Daten können bei Bedarf direkt von der Anwendung (1C, Excel usw.) mithilfe von API-Abfragen aus dem WebHMI gelesen werden.
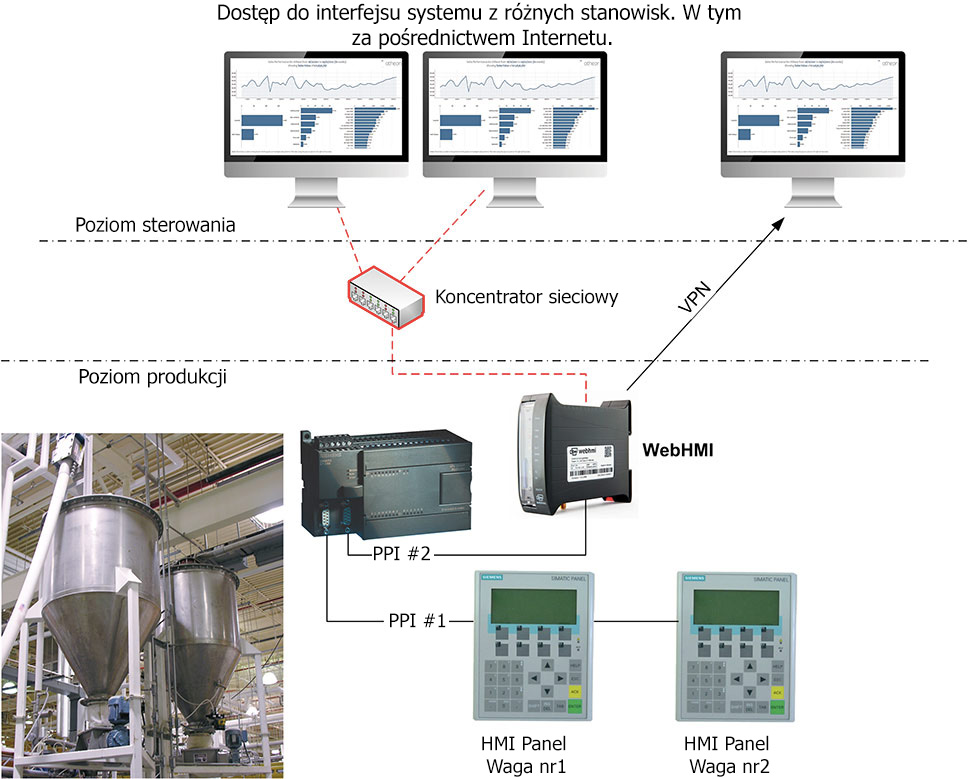
Die erhaltene Vorteile
- Die automatische Berichterstellung und die Möglichkeit, ein beliebiges Datum zu wählen, vereinfachte die Sortierung beim Anzeigen von Berichten erheblich
- Schnelle Konfiguration und Implementierung des Systems dank der integrierten Funktionen von WebHMI – Unterstützung für Kommunikationsprotokolle, den Mechanismus der Skripts und Ereignisse
- Die Entwicklung fand ohne Beeinflussung der vorhandenen Ausrüstung statt
- Integrierte Visualisierungstools und Grafiken ermöglichten uns nicht nur die Entwicklung einer intuitiven Oberfläche des fertigen Systems, sondern waren auch ein nützliches Werkzeug zum Debuggen und Analysieren des Prozesses während der Entwicklung
- Die Aufzeichnung der Arbeit der Waage steigerte schließlich die Disziplin und Verantwortung der Mitarbeiter. Diese Protokolle können von verschiedenen Mitarbeitern an verschiedenen Arbeitsplätzen eingesehen werden.
Przykładowy raport dozowania w chmurze WebHMI
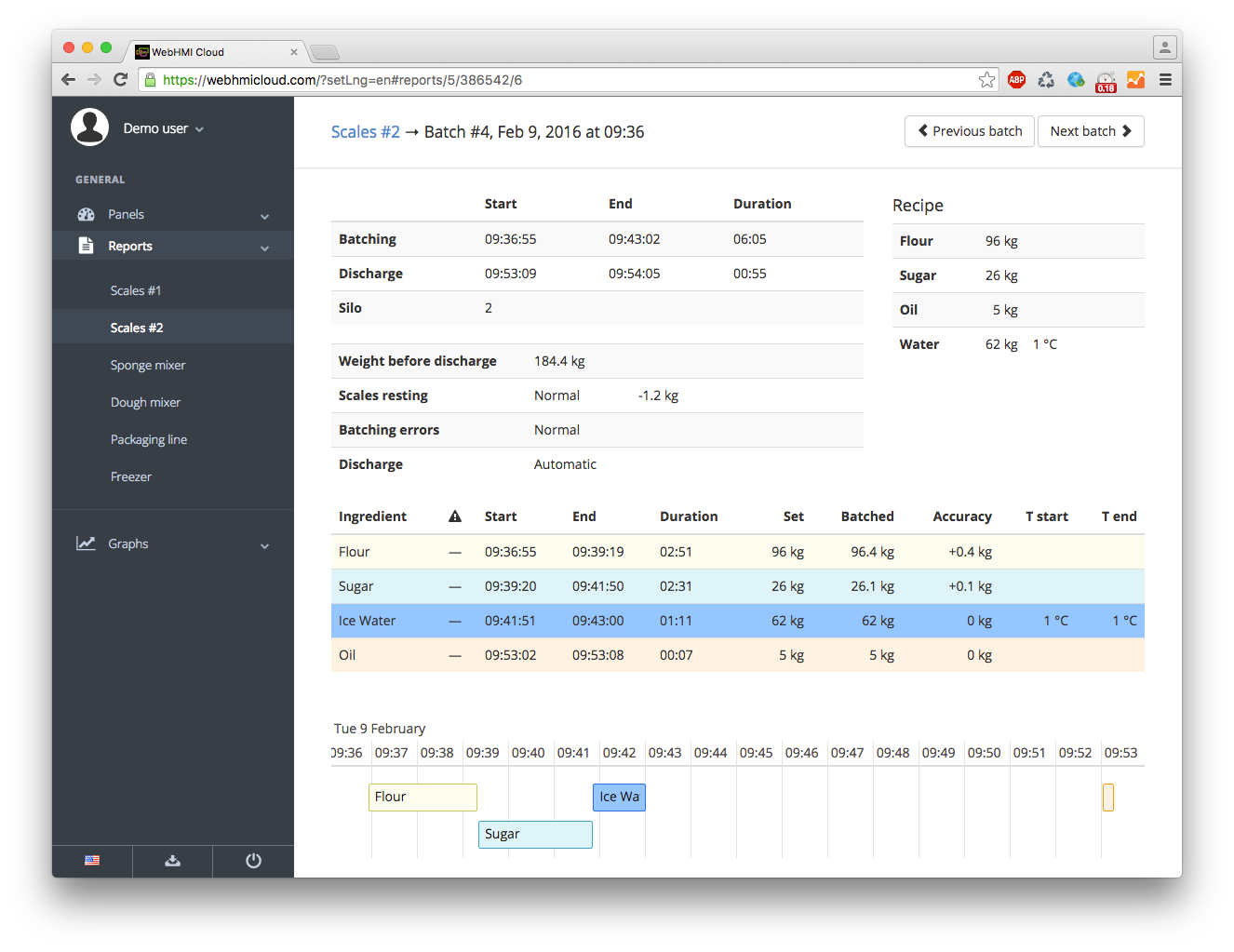
Die damit verbundenen positiven Vorteile der Verwendung von WebHMI waren auch:
- Die Möglichkeit, den Arbeitsprozess der SPS-Steuerungsgewichte von einem entfernten Arbeitsplatz des leitenden Ingenieurs aus über die integrierte Funktion „virtueller COM-Port“ zu programmieren und zu debuggen.
- Die integrierte Unterstützung für VPN ermöglichte es uns, den Fernzugriff auf das System vom Internet aus zu ermöglichen, sodass die Protokolle jederzeit und von jedem Ort aus bequem nicht nur für Bäckereispezialisten, sondern auch für das Top-Management dieses Bäckernetzwerks angezeigt und das gestraffte Rezept auf andere Bäckereien übertragen werden konnten
- Nach der Einrichtung des Knotens mit dem WebHMI-Integrationscontroller wurde der Mixer-Knoten zukünftig vollständig bereit, in die integrierte Überwachung und Verfolgung der hergestellten Produkte einbezogen zu werden – vom Startpunkt (Teig kneten) bis zur Verpackung und zum Versand. Alles, was Sie dafür brauchen, ist bereits an Bord von WebHMI – eingebettete Entwicklungstools, Kommunikationsfunktionen, Skripts, API-Unterstützung usw.